Hand Wrap vs. Machine Wrap
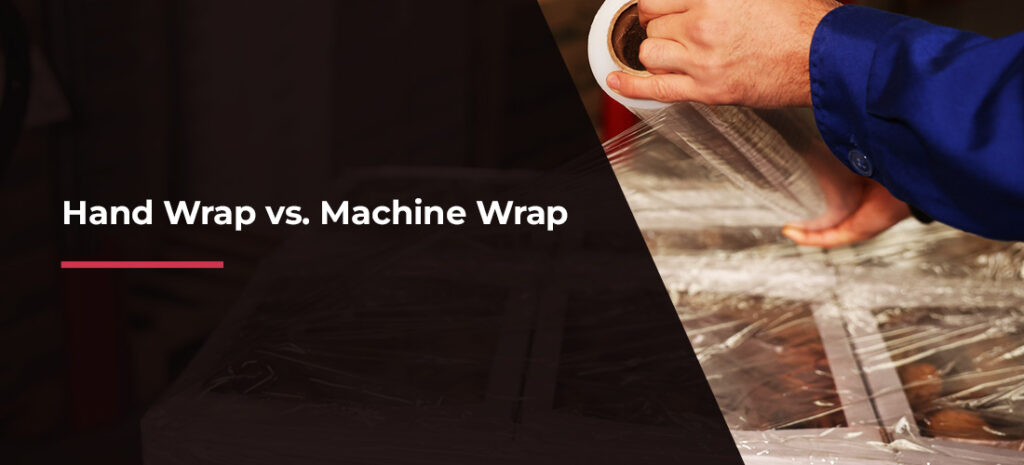
In industrial packaging, the debate between hand wrap and machine wrap is a pivotal discussion point relating to efficiency and cost-effectiveness. While both pallet wrapping methods offer distinct considerations and advantages, aspects like consistency, labor costs and overall packaging quality should be the deciding factors.
Understanding the basics of these methods is essential if your goal is to streamline packaging processes and maximize productivity while lowering expenses.
The Main Differences Between Hand Wrapping and Machine Wrapping
There are a variety of benefits and considerations when it comes to choosing between hand wrap and machine wrapping for your operations. While one method suits smaller, infrequent packaging needs, the other can optimize a larger operations workflow by wrapping multiple pallets a day.
Hand Wrap
Hand wrapping is wrapping packaging material manually using stretch film or tape. Unlike machine wrap, this option is labor intensive and can be time-consuming on large-scale operations. Additional differences include:
- Variable quality: Quality and consistency in manual applications vary depending on the operator’s skill and technique. Hand wrapping may lead to unreliable protection and load stability.
- Control and flexibility: Hand wrapping offers control and flexibility over the wrapping process as operators can adjust coverage and tension according to preferences or specific requirements.
- Small operation suitability: Smaller-scale operations often prefer hand wrapping as automation may be less cost- or space-efficient. If a business doesn’t wrap pallets frequently, hand wrapping may make the most sense.
Machine Wrap
Machine wrap or automatic stretch wrapping uses machinery to wrap and secure palletized loads with stretch film. It is different from hand wrapping in the following ways:
- Efficiency and speed: Automatic wrapping reduces wrapping time and labor costs, which leads to higher throughput and operational efficiency.
- Pallet protection: Machine wrapping helps to protect products against dust, moisture and other inconsistencies that can compromise products during transport or storage.
- Consistent quality: These systems produce consistent, uniform wrapping quality, increasing protection and load stability.
- Programmable settings: Stretch wrap machines often have programmable settings that allow you to adjust wrap tension, patterns and film stretch to optimize wrapping parameters.
- Scalability and integration: You can integrate these machines into existing production lines or material handling systems. They are scalable and suitable for medium to large-scale operations.
- Lower risk of injury: Eliminating manual wrapping tasks reduces the risk of employee injuries associated with repetitive motion and lifting, which creates a safer work environment.
Stretch Film Material Considerations
Stretch film, pallet stretch wrap or stretch wrap is a thin, stretchy plastic sheet material that wraps around boxes, pallets or products. This plastic film is made from linear low-density polyethylene (LLDPE) or a similar polymer with chemical resistance and high tensile strength. It is a reliable and versatile solution for packaging needs, offering benefits like elasticity, strength and protection for palletized goods during storage and transit.
For hand wrapping, stretch films come in various widths and thicknesses, most often from 10 to 18 inches. These variants allow for adaptability and flexibility in different packaging needs. They may come with easy tear-off edges and cling properties to simplify manual application.
Standard machine film comes in various widths, with the most common being 20″ and 30″. These films are made to withstand high-speed wrapping processes while maintaining consistent stretch and tension characteristics. They come in longer rolls and may have added benefits like better pre-stretch capabilities, which maximize film usage and optimize load stability.
Transitioning to Machine Wrapping: Considerations for Your Business
Switching to stretch-wrapping machinery and methods comes with various considerations. It is important to note that automating wrapping solutions can include automatic and semi-automatic machines. Automatic machines handle every step of the packaging process, while semi-automatic machines need an operator to place and remove pallets from the wrapping zone.
If you are shopping for stretch film wrapping equipment, there are two primary machines to consider:
- Turntable stretch wrappers: These machines use a turntable that spins the load while a dispenser with the stretch wrap moves up and down, wrapping the pallet.
- Straddle stretch wrappers: Straddle stretch wrappers move around while the pallet stays still. These machines work well with pallets that are heavy or imbalanced.
Labor Costs in the Packaging Industry
Labor costs have a significant impact on overall operational expenses. The median wages for packers and packagers are $32,920 a year. Manual wrapping processes contribute to this through higher labor costs and more time employees spend wrapping each pallet or load.
Automated wrapping streamlines packaging processes, reducing your dependency on manual labor. This leads to potential cost savings in labor expenses and better time usage for all employees as you can reallocate your team to more value-added activities like quality control or inventory management.
By wrapping pallets at a faster rate, you can achieve shorter lead times and better overall operational performance.
Packaging Machinery Parts and Maintenance
When you consider transitioning to machine wrap, it is important to understand how these machines work so that you can operate and maintain them efficiently. Parts that will require routine maintenance include:
- The film carriage: The film carriage is a crucial part of wrapping automation. It dispenses and applies the stretch film with accurate tension control. It’s best to check this part for film jams or tears consistently.
- The turntable: The turntable must rotate smoothly to position pallet loads accurately. Regularly check the drive mechanism, alignment and bearings for optimal performance.
- Controls and sensors: Controls and sensors monitor wrapping parameters like rotation speed, cycle counts and film tension. They must be calibrated regularly to ensure that they maintain accuracy and reliability.
It is also vital to partner with a stretch wrapping machinery supplier that helps your machines experience minimal downtime and operate seamlessly. The team at Viking Plastic Packaging, Inc. has the essential technical expertise to install, maintain and repair packaging equipment, helping to ensure these machines work according to your needs.
Partner With Viking Plastic Packaging, Inc. for Wrapping Machines
The decision between hand wrapping vs. stretch wrapping ultimately depends on factors like your production volume, efficiency goals and budget considerations. While hand wrapping offers flexibility, auto-wrapping systems offer speed, consistency and cost-effective solutions. You can find the right wrapping solution to optimize your productivity and packaging process by assessing your organizational needs.
Partnering with Viking Plastic Packaging, Inc. will help you get your product to market faster with cost-effective machines and equipment that are easy to install and service. We are ready to help you integrate the right premium packaging solutions into your manufacturing processes. Contact us today to explore machine stretch wrap benefits that will boost your operation’s packaging efficiency.